I live in and hunt the West. Its terrain is rugged; its weather, harsh. Traveling to a hunting camp or a public land access point — down rocky, bumpy, dusty roads — can take a toll on your equipment, if unprotected.
For several years, case technology has remained somewhat stagnant. Basically, you’re stuck with just two options — hard- or soft-sided. The hard case is great for the ultimate in protection, especially when air travel is required. However, their large, bulky design leaves them awkward to pack in a pickup truck or UTV, making them less effective in the field. On the other hand, a soft case provides the needed protection from the elements — dust, rain and snow — but not from a major jolt or drop. The industry needed a best-of-both-worlds product.
Along comes RUGID cases, hybrids of sorts, made of a durable waterproof PVC shell and closed-cell foam interior. I first heard of RUGID cases when they were unveiled at the ATA show in Indianapolis last January. Their display was a full row of hanging gun and bow cases, with a steady stream of water trickling onto and down the cases. It was eye-catching!
After learning more about the RUGID story, I have to admit, it was nice to hear and see a few new innovations introduced to case technology. Recently, I had the opportunity to interview Jeff Bruss, RUGID founder and bow case innovator, to learn more about RUGID’s products and innovations.
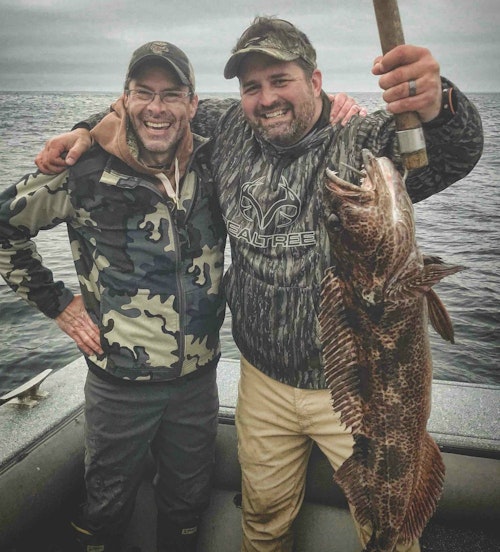
AB: Tell us how RUGID came to be.
JB: [Laughs] Well, the short story or the long one? A group of us had been heading out to Slater, Colorado, chasing elk and mule deer with our bows. Year after year we kept having the same problem — dust. The fine dust in the mountains was absolutely destroying our gear. Dust stuck in the peeps, stuck in the cams, stuck in pins; it was just awful.
We primarily use UTVs to get around, so our gear is always in the back. The dust constantly swirls up and around the bed. The first few years we used our soft cases. By day three or four the dust had made its way through the zippers. The zippers were barely functional and the cases were trashed. We even tried large garbage bags inside the cases and the results weren’t much better.
The following year I designed bow-sized bags made of waterproof canvas. I had my mother sew them up for us prior to leaving. I designed them with no zippers so we wouldn’t have any fail points. They worked pretty well, but didn’t close quite tight enough to keep all of the dust out. By the end of the week, the insides of the canvas bags were as dusty and dirty as the outsides, and so were our bows.
I was determined to design a case that would solve our problems for good. I wanted something that was as close to 100-percent dustproof as we could get, but still flexible enough to throw in the back of our Polaris Ranger. I was looking at the material they use for dry bags and got the idea to use it for a bow case. I figured the rubbery material would be dustproof and could be hosed off. The first prototype was a rubber rolltop case. It offered great dust protection, but didn’t have any padding to protect a bow from jostling in the back of the Polaris. Over a couple years I kept tweaking until it evolved into the case we have now.
AB: So your mom sewed the first cases?
JB: Well, yes and no. Once we moved to the PVC material, my mom’s skills were sadly obsolete. I don’t think she cried over that. We contacted some American manufacturers to help us, only to find out they all outsourced the actual manufacturing overseas. That led to long delays in making changes to prototype cases.
Rather than pay someone in the middle I just jumped on the Internet and found my own manufacturer. I would make drawings of what I needed, and we’d go back and forth via email until we were comfortable making one. It would take a few weeks to build a prototype and get it mailed to Wisconsin, then we’d commence to beating the crap out of it.
AB: How long did it take to come to the final design?
JB: It’s hard to say, but probably close to 2 years. The padding and the zipper were the hardest parts. We wanted a durable zipper that was tough enough to zip right through dust, but because the case was so big, the zippers were long and expensive. The zippers alone for the SCUBA type waterproof cases were running like $30 or more. The padding was originally just an open foam, which worked fine, but didn’t meet my hopes that we could make the entire case something that could be torn apart and cleaned.
AB: Elaborate on that, will you? The case can be torn apart and cleaned?
JB: Heck, yea, not just cleaned, but hosed or pressure washed. The bow case breaks down into four basic pieces — the waterproof PVC shell, a top pad, bottom pad and the crush-proof side padding. It’s all held in with Velcro. You can literally tear the entire case apart in about 10 to 15 seconds and shake it out, hose it out, and we’ve pressure washed them just to see how they hold up. You can even hose off the inner foam padding. It’s closed cell, so it doesn’t absorb water, and the soft cloth exterior dries super fast.
AB: It sounds like testing the cases was important?
JB: Of course. There’s nothing worse than equipment failing in the field. We tested the prototype cases for almost a year. The nice thing is, not only did it help us feel good about the product, but it led to most of the features we added. The tie-down straps, backpack straps that can clip on, and just overall design elements like the hard sidewalls to protect the bow — all were figured out by using the cases on actual hunts. We wanted a zero fail rate before we went to manufacturing. I still personally run one of the prototype cases with no problems — going on 3 years and lots and lots of dusty Ranger miles.
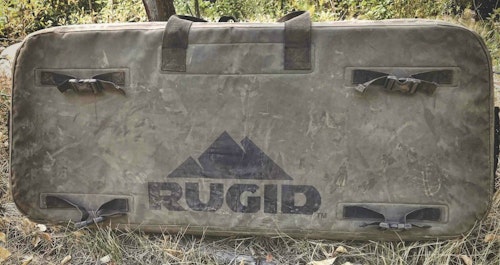
AB: You mentioned earlier that the zippers were one of the main testing and cost obstacles. You must have figured that all out?
JB: We did. We offer two zippers: a full waterproof SCUBA type zipper and a beefy water-resistant zipper. The only difference in those cases is the zipper, and of course the price. The full waterproof zipper adds about $50 to the retail cost. It’s a big, expensive zipper, and truly, 99 percent of hunters don’t need it. It’s overkill.
Because it’s a SCUBA zipper, it needs to be waxed and operates much stiffer than the standard zipper. We steer most dealers toward the basic case. It’s bulletproof. It also keeps the cost down to a more affordable price point.
AB: What is the price point on the bow cases?
JB: The standard case retails around $200 and the full waterproof comes in around $250, which we know is on the higher end of the soft case market. When you’re dropping $1,000, $1,500 or even $2,000 on a bow though, you want it to be protected, and that’s what our cases do. It’s an extremely durable soft case, providing essentially hard case protection in my opinion. It’s also built to last like a hard case. When was the last time you hosed out your soft case? Both inside and out? So are they expensive? No, I don’t think so. Nobody should be putting an expensive bow in a cheap case. Let’s just leave it at that.
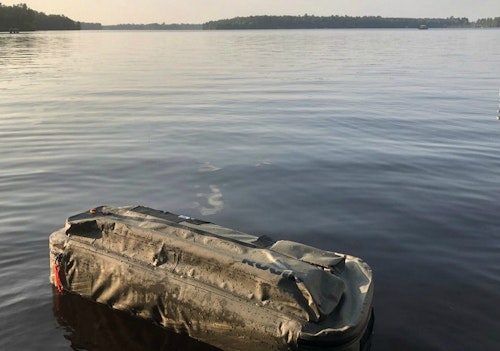
AB: I notice you say “we” and “our” a lot of the time when talking about the cases. Who is “we”?
JB: Well “we” for testing means my hunting buddies Chris and Dennis. Dennis is my brother-in-law, and he’s a guy that can break almost anything. He’s the person you never let borrow your new truck, or any truck for that matter. Chris is one of the best hunters I know. A seasoned mule deer, elk, whitetail and turkey guy who has taken our gear with him on trips all over the states. I wouldn’t be as comfortable with the testing if it weren’t for the help from those two. Back at the office, “we” means Brad and me. We work all of the sales, shipping and warehouse ourselves.
AB: So RUGID is just two employees?
JB: For now, yes, but obviously we’re sure hoping for more! It’s not even fulltime yet. Brad and I are still maintaining day jobs and work RUGID before, after and sometimes even during lunch breaks. I even get my wife and stepkids to help, so it’s truly a team effort.
AB: Anything you can share with us coming up in the future for RUGID?
JB: Actually, yes, we have a lot of good things going on. We have a utility patent pending on the cases to protect the unique way they are made and come apart. We hope to finalize those patents in the next few months. We are also working with some manufacturers of both bows and guns to potentially license or co-brand. We’ve had surprisingly strong interest from well-known brands, which we never expected to be working with this quickly out of the gate.
We have some new products rolling out this summer made with the same weathertight design and materials as our current products — a new crossbow case, binocular harness and duffel bags. We’re excited to keep building products that we know work better than the other stuff out there. I design, test and inspect it all myself and through friends, which I feel makes us different than the others. Our customer service and testing is what’s most important, because it has to be.
For more information on RUGID bow and gun cases, visit www.rugidgear.com.